Expertise : UHMPE
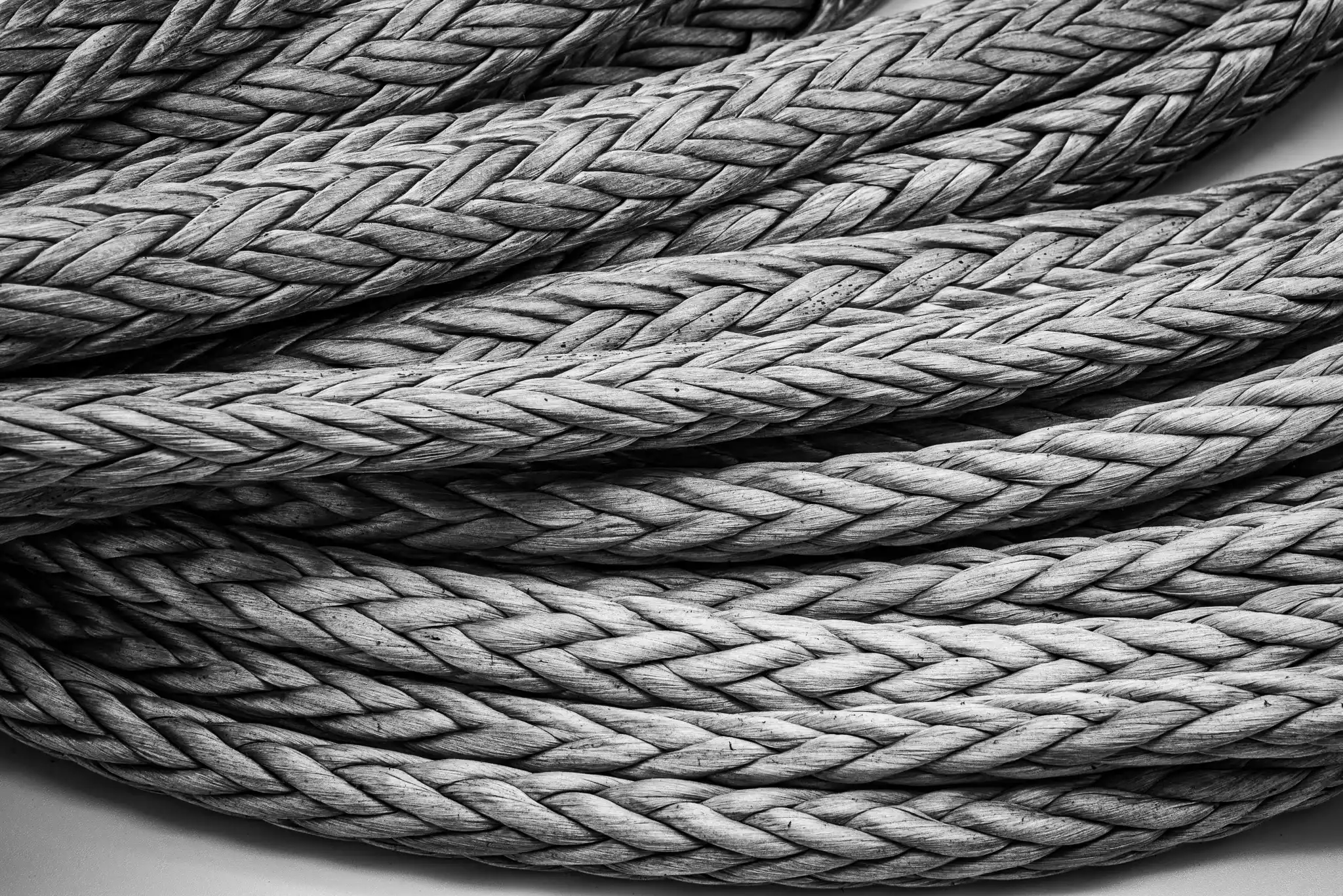
Dyneema et HMPE : quelles différences ?
Fibre issue du pétrole, le polyéthylène haut module (”high modulus polyethylene” en anglais) a été inventé par Albert Pennings en 1963. À masse égale, sa charge de rupture est bien supérieure à celle de nombreuses fibres. Il est peu sensible aux UV, à l’abrasion, aux forts rayons de courbure et aux milieux acides. Son défaut principal est sa sensibilité aux températures élevées et au fluage (allongement irréversible au-delà d’une certaine charge constante).
Le Spectra et le Dyneema sont des marques de polyéthylène haut module, respectivement commercialisées depuis 1983 et 1990 par les entreprises Honeywell et DSM Dyneema (qui s’appelle Protective Materials depuis son rachat par Avient, en 2022). Il en existe d’autres moins connues mais avec des propriétés similaires. Y a-t-il une différence entre ces marques et l’HMPE ? Sachant que HMPE signifie High Modulus Polyéthylène, vous vous doutez de la réponse.
L’abréviation HMPE est en effet un terme générique pour parler des fibres de polyéthylène haut module : c’est l’appellation chimique du matériau. Le Dyneema fait donc partie de la famille des HMPE.
Même si Dyneema est toujours le leader des cordages en poléthylène haut module sur le marché du nautisme, au point que la marque est devenue un nom commun dans ce milieu, il existe de nombreux autres fabricants de HPME qui n’ont pas de brevet ou de marque déposée parce qu’ils utilisent des procédés de fabrication moins coûteux.
Comment joue-t-on sur la résistance du polyéthylène haut module ?
En jouant sur la cristallinité du polyéthylène haut module, le process de fabrication de la fibre définit ses caractéristiques mécaniques. La résistance de cette dernière augmente avec la cristallinité. Pour faire simple, le polyéthylène haut module fait partie des thermoplastiques, des plastiques qu’on peut refondre. Si les chaînes de carbone de la fibre ressemblent à une assiette de spaghetti, sa résistance est moindre. Au contraire, plus les spaghetti sont alignés dans l’axe de la fibre, plus la résistance est importante.
Différents paramètres comme la température ou les techniques d’extrusion influent sur l’arrangement des chaînes de carbone en réseaux cristallins. L’extrusion, ”gel spinning” en anglais, est une technique aboutie qui consiste à mélanger les différents composants chimiques selon un protocole complexe au cours duquel le matériau fabriqué subit différents traitements et passe dans dans des filières (trous très fins), d’un diamètre maîtrisé, pour créer les fibres de polyéthylène haut module. Pour optimiser leur résistance, les fabricants peuvent également recourir à des traitements spécifiques, comme le pré-étirage à chaud : après leur passage dans les filières, les fibres sont étirées à une température proche de celle de fusion.
Les différences entre les process de fabrication de la fibre entraînent des écarts importants de résistance à diamètre égal mais aussi de sensibilité à l’abrasion et à la fatigue.
On peut supposer que la sensibilité à l’abrasion et à la fatigue est influencée par des facteurs comme la constance du diamètre ou la qualité de l’état de surface de la fibre, entre autres. Afin d’élargir sa maîtrise des matériaux, le bureau d’études d’Ino-Rope est en train de mettre au point une machine permettant de comparer la résistance à l’abrasion des cordages de différents fournisseurs.
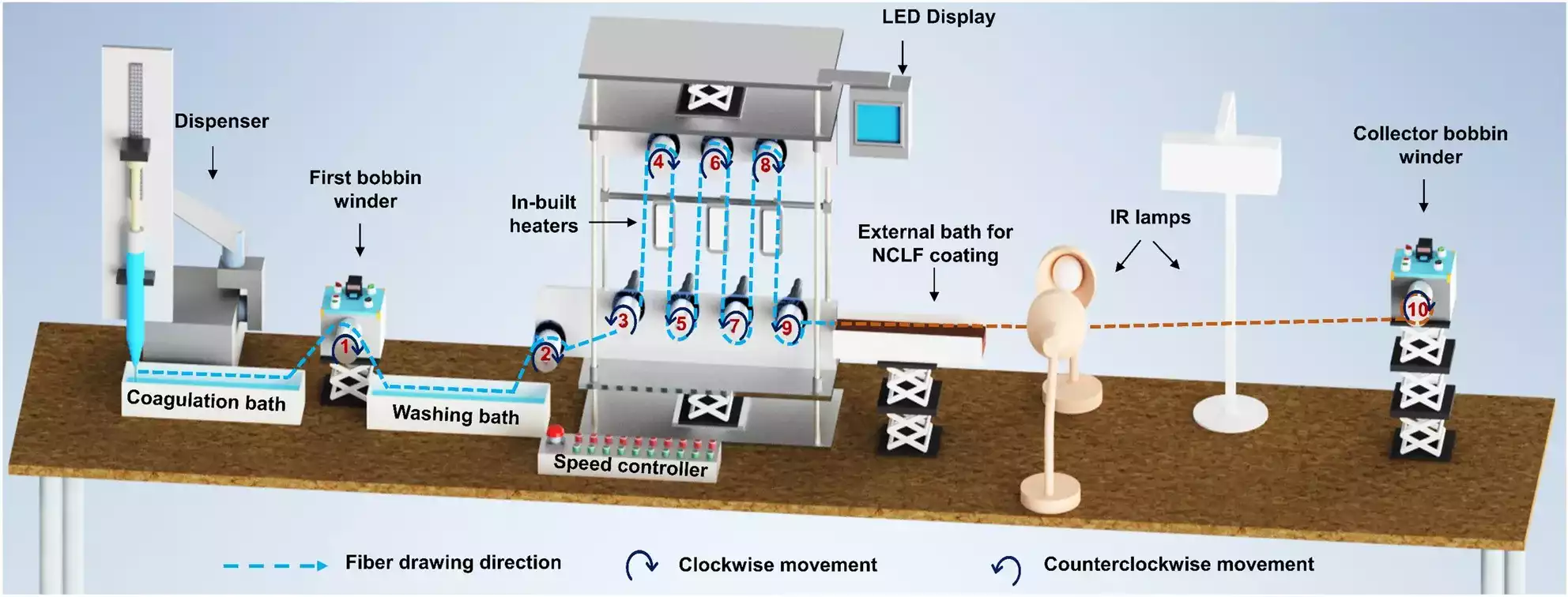
HMPE : Dyneema bas de gamme ou bon rapport qualité/prix ?
Parmi les alternatives au “gel spinning”, citons le “melt spin polyéthylène” mis au point par l’Université de Leeds au Royaume-Uni : la matière fondue est déjà entièrement mélangée et traitée lorsqu’elle passe dans les filières. Le process est certes très simplifié mais la résistance de la fibre est inférieure de 50%. La société américaine Celanese l’a exploité mais sans grand succès.
Développé par un japonais aux USA, le “Solid State Extrusion process” (extrusion à l’état solide) met en œuvre une poudre de polyéthylène haut module qui est écrasée et étirée jusqu’à obtention de fibres. Ces dernières tiennent 70% de la charge de celles fabriquées avec la méthode du gel-spinning. Des résultats plus satisfaisants avec un autre avantage : une perte de matière moindre car le process ne comprend pas, contrairement au “gel spinning”, l’élimination dans des bains des composés chimiques qui se sont déposés sur les fibres au cours de leur fabrication. Enfin, le prix de la fibre obtenue par extrusion à l’était solide est inférieur de 50%.
Les procédés de fabrication plus simples que le “gel spinning” ne permettent pas de produire des fibres aussi performantes (diamètre supérieur à résistance égale, résistance à l’abrasion et à la fatigue inférieure). Le terme HMPE est ainsi souvent associé, à tort, à du “Dyneema bas de gamme” (rappelons que l’abréviation HMPE désigne n’importe quelle fibre de polyéthylène haut module).
L’emploi de cordages en HPME tressés à partir de fibres HPME issues de process de fabrication simplifiés est néanmoins pertinent, certains fabricants proposant du HMPE à un rapport qualité/prix très intéressant.
Les applications des cordages en HMPE chez Ino-Rope
En fonction du cahier des charges de son client, Ino-Rope qualifie le type de fibres et de structures de cordage adapté. Si l’application à laquelle le cordage est destiné impose une résistance importante mais avec un critère de limite d’encombrement (diamètre maximal), il est par exemple possible que le recours à un cordage spécifique de la marque Dyneema s’impose. Si le câble textile est destiné à l’industrie et que le critère du coût prime sur celui du rapport diamètre/résistance, l’usage d’un cordage en HMPE permet de répondre au besoin de l’utilisateur.
Tout l’enjeu repose sur la qualification du cordage : grâce à son expertise, Ino-Rope est capable de dimensionner précisément le diamètre d’un cordage en HMPE selon son usage.
afin de “compenser” l’écart de qualité avec un cordage en polyéthylène haut module “haut de gamme”. Un coefficient de sécurité important est appliqué afin de garantir la fiabilité du produit tout en respectant des coûts raisonnables.
Une logique qu’Ino-Rope a l’habitude de pratiquer avec le Dyneema puisque (hormis le DM20 mais qui coûte très cher) n’importe quelle fibre de polyéthylène haut module est sensible au fluage, qui est un allongement irréversible sous charge constante. Le fluage impose l’application de coefficients de sécurité afin que le cordage ne travaille pas à une charge qui, maintenue trop longtemps, “déclencherait” le fluage (un pic de charge n’entraîne pas de fluage).
Le bureau d’études d’Ino-Rope mène par ailleurs des tests (il y a encore trop peu de données scientifiques qui permettent d’expliquer les différences de propriétés des fibres) et effectue un contrôle qualité rigoureux, une étape qui peut parfois faire défaut chez certains fabricants avec des lots inégaux. Ino-Rope a ainsi sélectionné les meilleures références de cordages en HPME, notamment le Super-12 de la corderie Southern Ropes, et continue d’élargir son catalogue pour proposer à ses clients les solutions de câbles textiles les plus adaptées.
Un besoin
spécifique ?
INO-ROPE s’engage à fournir des solutions à base de cordage innovantes et de haute qualité, soutenues par une expertise inégalée et un dévouement à la satisfaction du client.
Contactez-nous pour découvrir comment nous pouvons vous aider à réaliser vos projets les plus ambitieux.