Acoustic Study Buoys – Custom Line Kits for Sustainable Measurements
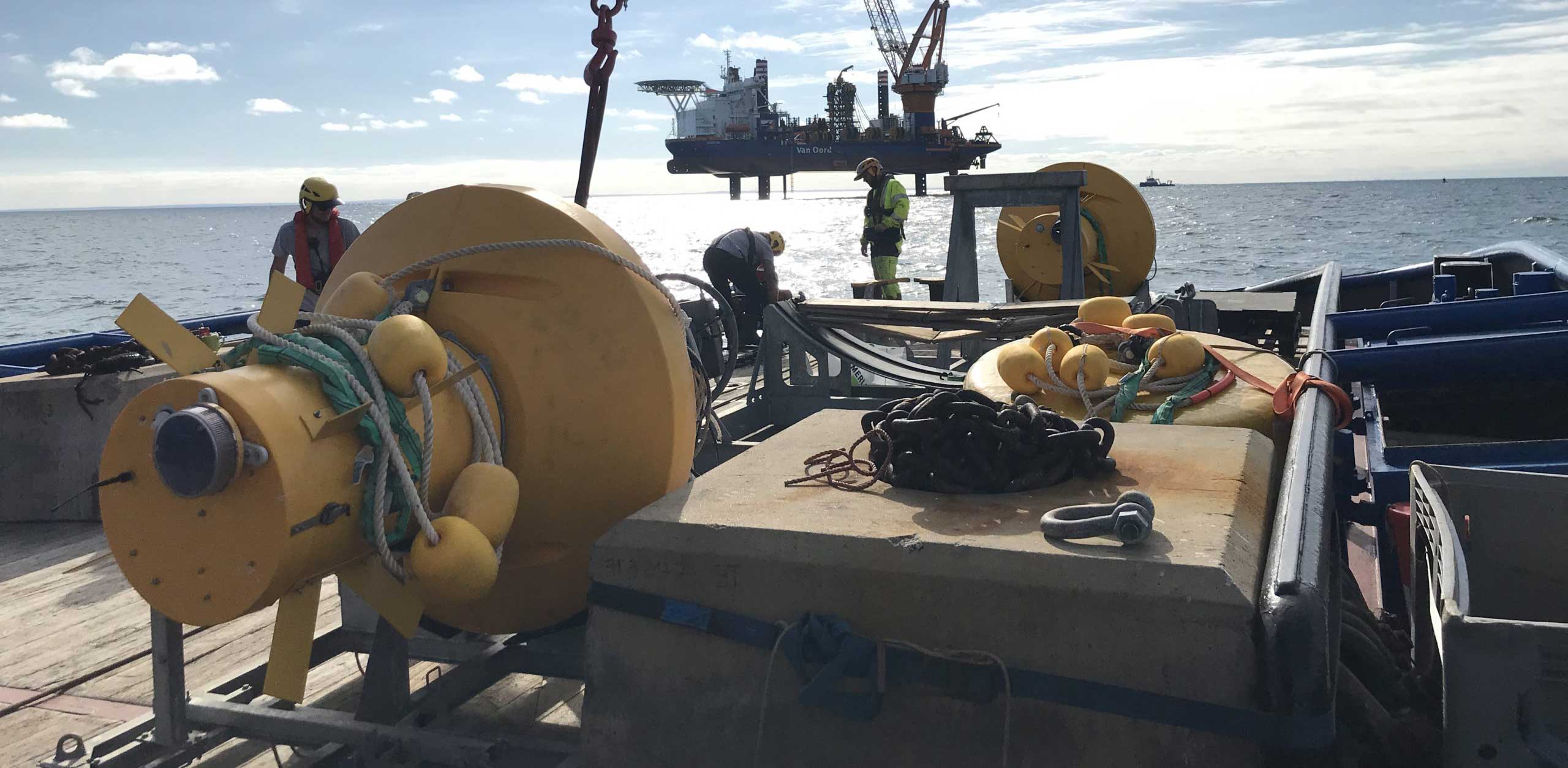
An environmental and logistical challenge met with an innovative solution
Ino-Rope, an expert in high-performance mooring and anchoring solutions, is proud to have assisted SOMME, a meteorological measurement company, in designing and manufacturing custom line kits for its acoustic study buoys. This project addresses both environmental and logistical challenges: reducing the impact of measurements on the marine environment and optimizing the installation, handling, and maintenance of the lines.
A demanding context: frequent measurements and minimizing environmental impact.
SOMME regularly conducts short-term acoustic measurement campaigns (2 months to 3 years maximum) at sea. These campaigns require the use of acoustic buoys anchored by lines, posing two major challenges:
- Environmental impact: The accumulation of lines at sea contributes to marine pollution.
- Logistics The frequent installation, handling, and maintenance of lines represent significant costs and time constraints.
A custom and sustainable solution: reusable line kits
Ino-Rope suggested an innovative solution to SOMME: custom line kits composed of 5 elements:
- Dyneema protective bottom line
- Subsurface buoy
- Simple “intermediate” line
- Sub-buoy line with anti-fouling protection
- Floating line with signaling
These kits, produced in series of 20 units (totaling 100 elements), allow for the design of around twenty lines. The system of attachment to steel shackles facilitates the assembly of lines according to the specific needs of each campaign.
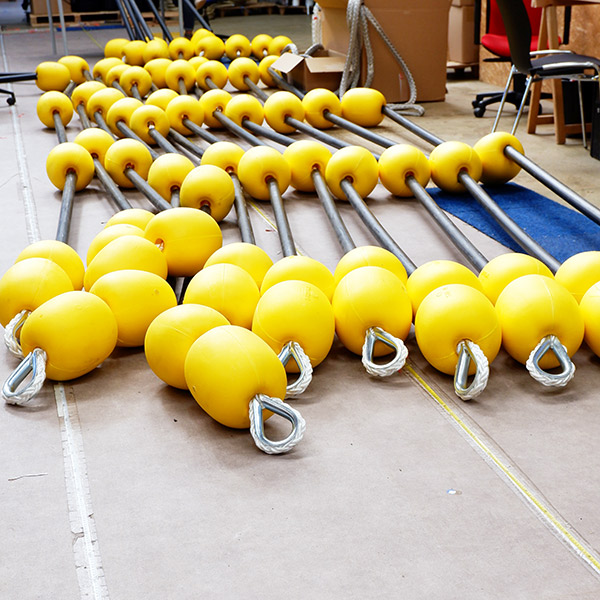
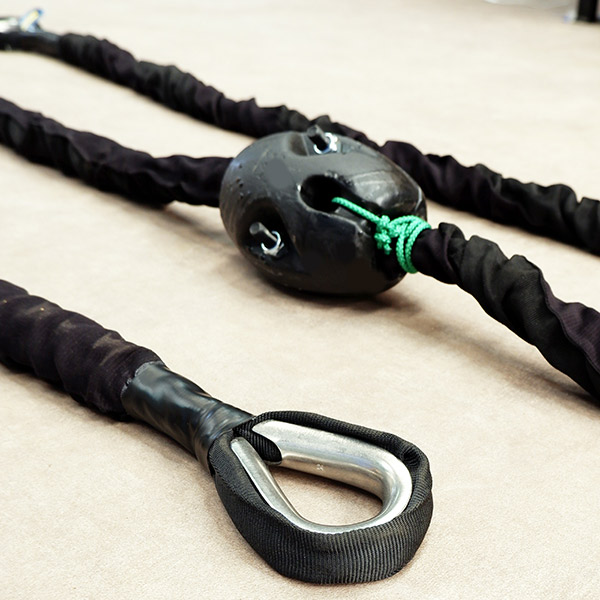
A circular and sustainable approach
Beyond modularity and ease of use, the Ino-Rope solution stands out for its sustainable approach:
- Material reuse The kits incorporate Dyneema lines from previous campaigns and production remnants, minimizing waste and optimizing costs.
- Material longevity: Dyneema has a lifespan of at least 10 years in marine environments, allowing for multiple uses of the kits.